

Wiley, Hoboken (2006)Īltmann, D., Praher, B., Steinbichler, G.: Simulation of the melting behavior in an injection molding plasticizing unit as measured by pressure and ultrasound measurement technology. Tadmor, Z., Gogos, C.G.: Principles of Polymer Processing, 2nd edn. Hayward, A.T.J.: Compressibility equations for liquids: a comparative study. Hanser, Munich (2012)Īrrhenius, S.: Über die Dissociationswärme und den Einfluss der Temperatur auf den Dissociationsgrad der Elektrolyte. Osswald, T.A., Menges, G.: Material Science of Polymers for Engineers, 3rd edn. Rauwendaal, C.: Polymer Extrusion, 5th edn.
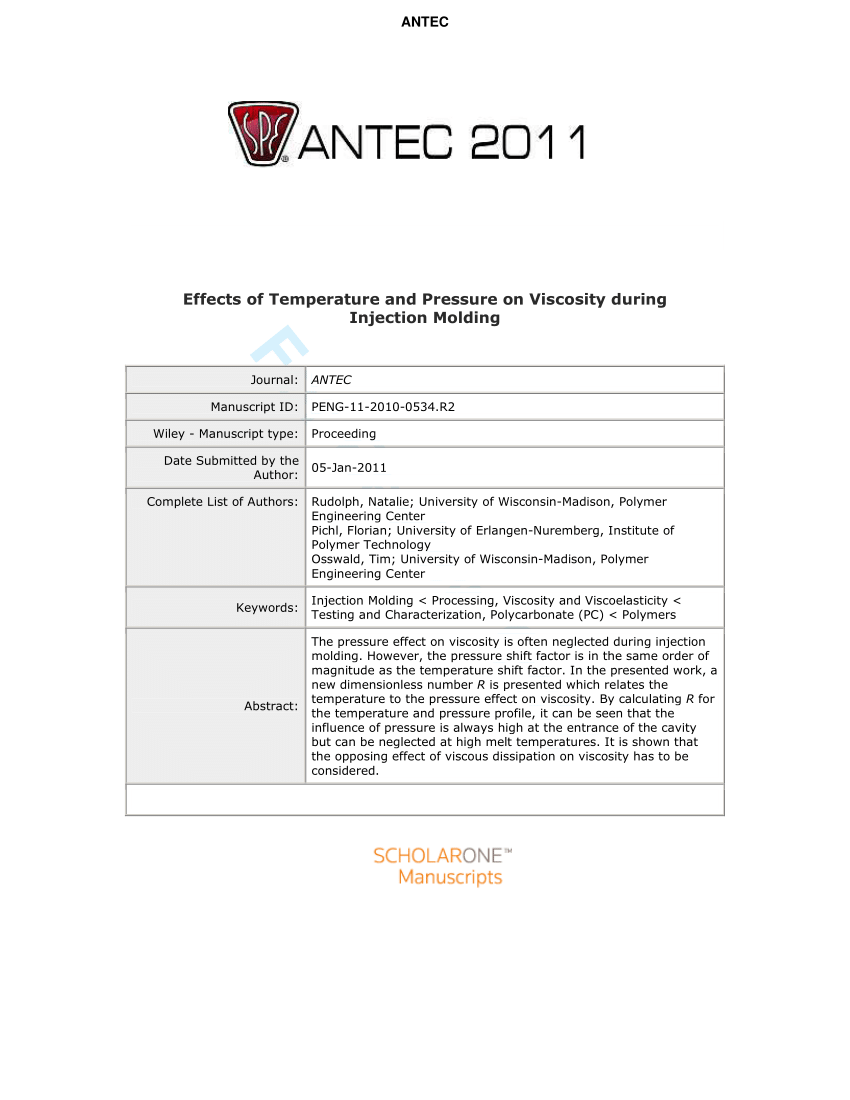
Kim, H.T.: Apparatus for extruding polymeric material. US Patent 3698541 (1971)ĭray, R.F., Lawrence, D.L.: Apparatus for extruding plastic material. Swiss Patent 363149 (1959)īarr, R.A.: Extruder, or extruder-like melting apparatus. Rauwendaal, C.: Extruder screws with barrier sections. Maddock, B.H.: Visual analysis of flow and mixing in extruder screws. Praher, B., Goldmann, M., Steinbichler, G.: Inline melt homogeneity measurement in injection molding. Our simulations show good agreement with experimental studies conducted with various screw sizes and barrier configurations. The axial screw motion during the plasticizing process and the idle time during the injection and holding phase are considered as well. Melting performance, pressure build-up and temperature distribution can be calculated numerically based on physical models and finite-difference approximation schemes. The three-dimensional helix shape of the screw channel consisting of feed, barrier and metering section can be approximated via an unwound screw channel. Besides a comparative view of different screw designs, we focus on modelling the plasticizing process in barrier screws using our recently developed software S3 ( Screw Simulation Software) to investigate both the melting and the melt conveying process in more detail. We present different high-performance screw concepts for various applications in the injection molding industry. Short cycle times in the injection molding process due to fast and effective cooling of the molds extend the demands for novel screw concepts starting from double-flighted screws and leading to barrier screws with dispersive and distributive mixing elements.
